Preparing the facility: cleaning the equipment and the building
The equipment must be clean (including high-pressure cleaning of skips and grain handling equipment….).
Buildings too! Insects do not come from the fields, but from storage facilities from one campaign to the next. They concentrate where there is dust, breakage, etc. It is therefore essential to :
- clean the inside/outside of the cell walls, and if possible the framework, especially if it is made of wood.
- vacuum up and immediately destroy dust and plant waste
- take care to clean the floor of flat cells
If possible, use smooth floors. In the event of insect proliferation, in addition to cleaning, insecticide treatment will be carried out on the equipment AND in the premises. There are, of course, organic treatments that we recommend.
Grain reception
When grain is contaminated with decay, it should not be passed through the handling system or stored to avoid contamination of the whole plant. It is advisable to contact your storage organisation to define an acceptable strategy.
Grain should be stored clean and sampled. If you can, as soon as harvesting begins, a few measures can be taken to limit the risk of insects appearing. To do this, you really need to adjust the speed of the threshing drum, the threshing/counter-threshing arc and the air flow to the cleaning tables (read your instructions).
The idea is also to harvest as many ripe grains as possible with a moisture content of less than 15%, and less than 9% for oilseeds.
Sorting and cleaning grains
To optimise grain cooling and limit the risk of insects, it is important to store clean grain.
- pre-clean the grain when it is put into storage
- sort and clean the grains, choosing the right size of grate. Sometimes, in the case of very dirty grains, it is important or even necessary to make a second pass. There are cleaners/separators
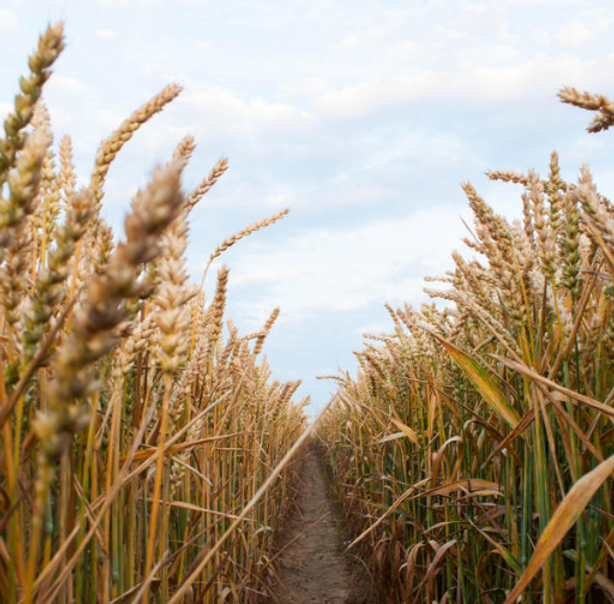
Drying grains
If you have harvested wet grains, drying is essential.
- clean the dryer between each species to avoid the risk of contamination between grains (and limit the risk of fire)
- harvest a quantity equivalent to the dryer throughput to avoid pre-storage of wet grain
- pre-clean the grain before passing through the dryer. Removing large wet impurities results in fuel savings of around 3% for every 1% of waste removed. In addition, clogging of the dryer during the campaign is reduced and fire safety is improved.
- Set temperatures correctly
Cooling grains by ventilation
The best way to combat insects is to lower the temperature of the grain masses.
- Ventilation is essential as soon as the crop is harvested. The temperature of the grain must be brought down as quickly as possible from 30-35°C to 20-22°C. At 20°C and above, the risk of insects developing is reduced and the grain will keep longer.
- ventilate when the temperature difference between the air and the grain is between 7 and 10°C
- ventilate until the top 50 cm has cooled down completely
Installing a thermostat and an hour meter to control the ventilation more than helps.
Controlling grain predators
Bird control :
- check that openings are sealed
- install netting (max. 18mm mesh)
- darken buildings as much as possible
Rodent control:
- clear the area around buildings
- remove anything that could be used as shelter (wood, scrap metal, old equipment, etc.)
- close off openings: drains, ventilation, etc. (with wire mesh)
- locate droppings
- call in a specialist company
If insects are visible
Good cooling ventilation should be the basic rule of insect control.
Only in the event of a confirmed infestation should the grain be treated by fogging. The product is sprayed at high pressure by compressed air through a poisttioned nozzle onto a foot of steam electricity or a screw head.
Pets
Cats are a great way of controlling rodents, but… they often leave their faeces, and the same goes for dogs.
Source of the article TECHN’ITAB grandes cultures ‘stockage à la ferme des grains issus de l’agriculture biologique’ June 2006, itab.asso.fr